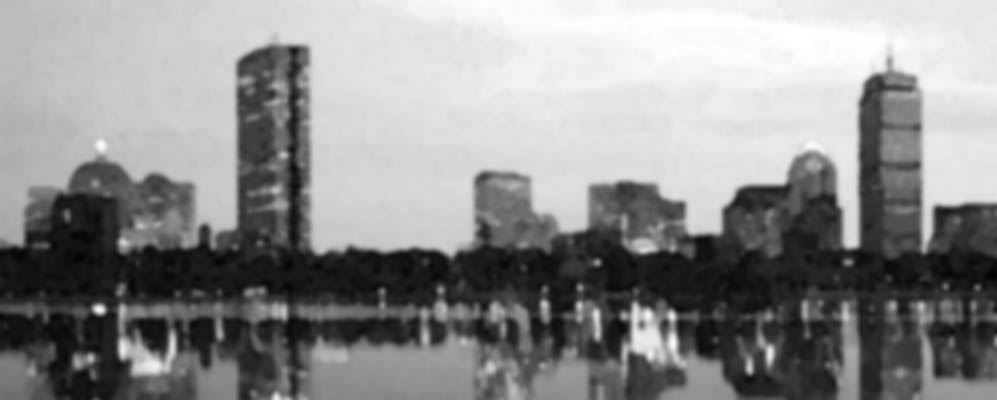
News / Events
Fraunhofer CMI - Center for Manufacturing Innovation
Events 2016
-
Biodefense Summit
June 29, 2016 • Baltimore, MD
Alexis Sauer-Budge, Ph.D., Senior Research Scientist, at Fraunhofer CMI gives a talk on "Rapid Phenotypic Methods for Diagnosing Infections and Antibiotic Susceptibility Testing."
-
Hannover Messe
25-29 April, 2016 • Hanover, Germany
»Get new technology first« Meet Fraunhofer CMI at the HANNOVER MESSE, the world's leading trade fair for industrial technology. Fraunhofer CMI's latest research in custom automation projects and biomedical engineering will be found at the booths of Fraunhofer USA B60 and Fraunhofer IPT C18.
-
SPIE Photonics West Conference
February, 2016 • San Francisco, CA
Fraunhofer CMI's research in the field of Biomedical Spectroscopy, Microscopy, and Imaging, and Photonic Therapeutics and Diagnostics, will be represented by their research collaborators of the BU-Alliance and the CFTCC.
News
-
Fraunhofer CMI presents low-cost, real-time, continuous flow PCR system for pathogen detection
Mar 31, 2016 • by Fraunhofer CMI
Fraunhofer CMI (USA) and their partners from Fraunhofer IPT (Germany), as part of the ML2 consortium, aim to create low-cost pathogen diagnostics by combining microfluidic and electronic layers into a single device.
A RISING THREAT TO HUMAN HEALTH
Bacterial resistance to antibiotics is escalating and represents a significant health threat to the human population. These alarming circumstances have largely resulted from the current clinical practice of prescribing broad-spectrum antibiotics first and identifying whether or not they are needed or even useful later—after the standard 18-48h culture. When it is critical to know whether or not a particular pathogen is causing disease, as is the case for outbreaks or epidemics, clinicians and laboratories turn to a rapid nucleic acid test (NAT) that can identify a pathogen within hours. However, NATs require specialized lab space, expensive reagents, and extensively trained technicians to appropriately conduct the assays. To reduce costs, labs process samples in batch once-per-day making the effective turn-around-time 24h, by which time patients have left the clinic, often with broad-spectrum antibiotics in hand. In order to stem the tide of antibiotic resistance and preserve this critical resource for the correct patient, rapid point-of-care diagnostics are essential.OUR SOLUTION
For more information:
At Fraunhofer CMI/IPT, we are developing a NAT demonstrator chip that can identify pathogens within 20 minutes and can be produced at low-cost thus eliminating batch processing altogether. Our demonstrator chip works by introducing the pathogen sample with NAT reagents into the microfluidic channel of a small 3 cm x 5 cm thermoplastic chip. The genetic content of the sample is amplified as it moves through the microfluidic channel that traverses two heating zones. Within 20 minutes, the presence of the pathogen is detected on-chip by fluorescence. The final chip itself will incorporate the heating elements and microfluidics into separate layers and will be laminated en masse by ML2 industrial scale roll-to-roll manufacturing methods.Press: US Fraunhofer Center Develops Method for Mass Manufacture of Low-Cost Continuous Flow PCR Devices, Mar 30, 2016, Madeleine Johnson for Genome.
Publication: Fernández-Carballo, L. B.; McGuiness, I.; McBeth, C.; Kalashnikov, M.; Borrós, S.; Sharon, A.; Sauer-Budge, A.F. "Low-cost, real-time, continuous flow PCR system for pathogen detection", Biomed Microdevices (2016) 18:34; DOI 10.1007/s10544-016-0060-4.
-
Custom Automation for Sheet Metal Forming
Mar 1, 2016 • by Fraunhofer CMI
A high precision custom automation project developed by Fraunhofer CMI for an industrial company from the consumer products industry.
Traditionally, sheet metal may be formed into various shapes by hammering the metal on various anvils. This labor intensive, physical process requires master craftsmen and is normally only suited to low volume production or prototype work. As products transition to higher volume, stamping dies are fabricated to greatly speed the process and reduce cost in quantity. However, there are some products which can benefit greatly from the unique metallurgy that is produced by individual hammer strikes.Applying automation to this labor intensive process has been difficult due to the wide variation in the size, shape, and weight of products that are manufactured. The different hammer patterns require a flexible holding system to allow nearly all of the sheet metal surface to be reached. Furthermore, the hammering can cause some metal to deform in process in an unpredictable way. This form is corrected in subsequent processes, but an automated hammering system must accommodate this changing shape.
The Fraunhofer CMI has collaborated with its customer to develop a new impact hammer system for the production of a wide variety of sheet metal shapes. Two impact hammers are incorporated into a work cell serviced by one loading robot. The work cell allows unattended processing, with the robot loading incoming metal blanks from material handling carts, and outputting processed parts on similar carts.
The hammers themselves use a high performance hydraulic ram system for the hammering action. The hammer can cycle in excess of 10 strikes per second, limited by the amount of positioning required between each strike. Interchangeable anvils can provide different hammering characteristics. The hammering force is programmable, as are all crucial process parameters such as the pattern and metal thickness. The operator needs to only select the appropriate program from a menu of choices. Manipulation of the sheet metal blank is accomplished with a robust, multi-axis positioning system using linear and rotary axes to provide full access to the metal surface for multiple shapes while withstanding the intense vibration and forces of the hammering operation. The work cell successfully processes the products while greatly reducing the required labor.For more information about Fraunhofer CMI's capabilities in this field: Custom Automation Services.
-
Fraunhofer CMI and their research collaborators present their latest work in biomedical engineering at the SPIE Photonics West 2016 conference
Feb 1, 2016 • by Fraunhofer CMI
Around 20,000 visitors are expected at the SPIE Photonics West 2016 conference in mid-February 2016 in San Francisco, CA, to see the latest research and development in the field of laser, photonics, and biomedical optics. The work of Fraunhofer CMI's engineers and scientists will be presented at the SPIE Photonics West BiOS EXPO in the conference program tracks of Biomedical Spectroscopy, Microscopy, and Imaging and Photonic Therapeutics and Diagnostics.
Tuesday, 16 February: Biomedical Spectroscopy, Microscopy, and Imaging
Fraunhofer CMI and their research collaborators of the BU-Fraunhofer Alliance for Medical Devices, Instrumentation and Diagnostics collaborate to accelerate promising technologies from the research stage to the marketplace. At the conference they will be presenting their project of "A wearable continuous-wave optical device for continuous monitoring during neoadjuvant chemotherapy infusions" in the session for »Optical Diagnostics and Sensing XVI: Toward Point-of-Care Diagnostics« as a new method for optical blood oxygenation measurements.
Researchers: Fei Teng, Boston Univ. (USA); Timothy Cormier, Alexis Sauer-Budge, Fraunhofer CMI/Fraunhofer USA, Inc. (USA); Darren M. Roblyer, Boston Univ. (USA)
Saturday 13, February: Photonic Therapeutics and Diagnostics
Fraunhofer CMI and The Center for Future Technologies in Cancer Care (CFTCC) at Boston University collaborate based on the translational core of the BU-Fraunhofer Alliance model. Together they worked on the "Design of an everting balloon to deploy a micro endoscope to the fallopian tubes" as a contribution to new »Diagnosis and Treatment of Diseases in the Breast and Reproductive System II« in Gynecology.
Researchers: Molly Keenan, Caitlin Howard, Tyler Tate, The Univ. of Arizona (USA); John Black, Glannaventa, Inc. (USA); Urs Utzinger, Jennifer K. Barton, The Univ.of Arizona (USA)
-
Fraunhofer CMI addresses the president's national action plan to combat antimicrobial resistance
Jan 4, 2016 • by Fraunhofer CMI
The rise of bacterial resistance intensifies the need for rapid phenotype-based antibiotic susceptibility tests (ASTs) in order to safeguard our drugs of last resort. Standard ASTs are based on bacterial growth inhibition in the presence of antibiotics that take multiple (8-24) hours to complete. Fraunhofer CMI's biomedical researchers have developed a novel AST on a microfluidic platform that relies on the stress-activation of biosynthetic pathways to accelerate the action of antibiotics.
Fluid is passed at high speeds over bacteria immobilized on the bottom of a microfluidic channel. In the presence of stress and antibiotic, susceptible strains of bacteria die rapidly. However, resistant bacteria survive these stressful conditions. As compared to standard AST methods, the rate-limiting step - bacterial growth - is omitted during antibiotic application. The technical implementation of the method relies on several innovative techniques, including the use of culture media flow for mechanical stress application, the use of enzymes to damage but not kill the bacteria, and the use of microarray substrates for bacterial attachment.
This novel AST platform can successfully distinguish susceptible and resistant strains in less than an hour. Feasibility has been proven by testing a panel of Staphylococcus aureus strains against oxacillin. However, antibiotics with targets other than the cell wall have also been shown to work in our platform on this timeframe. Experiments with other Gram-positive and Gram-negative strains have been promising, and will be published in due course.
"This technique will pave the way for researchers to explore how bacteria respond to stress, and will impact the development of novel rapid diagnostics and the discovery of new drugs" says Dr. Alexis Sauer-Budge, Senior Researcher at Fraunhofer CMI.
The microfluidic AST platform is presented in the Journal of Visualized Experiments (JoVE): Kalashnikov M, Campbell J, Lee JC, Sharon A, Sauer-Budge AF. Stress-induced Antibiotic Susceptibility Testing on a Chip. J Vis Exp. 2014(83). PubMed PMID: 24430495.
-
Fraunhofer CMI has developed a 3D Bioprinting System for the next Generation of "Bottom-Up" Tissue Engineering
Dec 1, 2015 • by Fraunhofer CMI
The list of patients in dire need of organ transplants grows longer every day. Patients who are fortunate enough to find a 'match' still struggle with immunosuppressive therapy and ultimate organ failure. The goal of 3D bioprinting is to precisely place cells in environments that trigger their growth into fully functional tissues and organs. Fraunhofer CMI, and others involved in this effort, are working towards the ultimate goal of bioprinting the patient's own cells into a new and healthy replacement organ.
Fraunhofer CMI's latest achievement in this field, was the development of a three-dimensional (3D) bioprinting system capable of multimaterial and multiscale deposition to enable the next generation of "bottom-up" tissue engineering. This area of research resides at the interface of engineering and life sciences, requiring an interdisciplinary team of engineers and scientists. Their work entails the design and implementation of diverse elements: a novel hydrogel-based bioink, a 3D bioprinter, automation software, and mammalian cell culture.
Fraunhofer CMI's bioprinter has three components uniquely combined into a comprehensive tool: syringe pumps connected to a selector valve that allow precise application of up to five different materials with varying viscosities and chemistries, a high velocity/high-precision x–y–z stage to accommodate the most rapid speeds allowable by the printed materials, and temperature control of the bioink reservoirs, lines, and printing environment. Our custom-designed bioprinter is able to print multiple materials (or multiple cell types in the same material) concurrently with various feature sizes (100 μm–1 mm wide; 100 μm–1 cm high). One of these materials is a biocompatible, printable bioink that has been used to test for cell survival within the hydrogel following printing. Hand-printed (HP) controls show that our bioprinter does not adversely affect the viability of the printed cells.
Fraunhofer CMI reports the design and build of the 3D bioprinter, the optimization of the bioink, and the stability and viability of the printed constructs in their publication "Multimaterial and Multiscale Three-Dimensional Bioprinter" in the Journal of Nanotechnology in Engineering and Medicine.
The researchers are currently in the process of bioprinting blood vessel precursors using both smooth muscle cells and endothelial (blood vessel wall) cells. They also work in the area of osseointegration of hip implants and have successfully bioprinted scaffolds that trigger osteoblasts (bone cells) to deposit new calcium mineral.
Fraunhofer CMI can be contacted to pursue collaborative research projects involving tissue engineering or bioink development. Industrial organizations looking to incorporate bioprinting into their research portfolio can also reach us to pursue custom instrumentation for tissue engineering solutions.
-
Fraunhofer CMI has been awarded MLSC Cooperative Research Matching Grant
June 26, 2015 • MLSC Press Release | Fraunhofer CMI
The Cooperative Research Matching Grant Program by Massachusetts Life Sciences Center (MLSC) is designed to promote industry-academic research collaborations, support translational research, and accelerate the commercialization of promising products and services.
Dr. Alexis Sauer-Budge, of Fraunhofer CMI, is one of the research partners that were authorized to receive a Cooperative Research Matching Grant (grant amount: $225,000) in June 2015. Fraunhofer CMI is partnering with AdvanDx to propose the development of a rapid and low cost system for positively identifying the microbes causing sepsis, which would then lead to faster treatment. Sepsis accounts for 40% of all ICU costs, making it the most expensive condition treated in US hospitals. According to the federal Agency for Healthcare Research and Quality, sepsis cases cost more than $20 billion to treat in 2011.
SOURCE: Massachussets Life Sciences Press Release
-
Fraunhofer CMI Developed Artificial Hand for Minimally Invasive Surgery
May 13, 2015 • by Fraunhofer CMI | Fraunhofer USA News
Over the past several decades, minimally invasive surgery has become more prevalent because it does not require major incisions to the patient, allows for quicker healing, reduces post-operative pain, and may reduce wound complications. However, in comparison to open surgery, existing laparoscopic tools still limit the surgeon's dexterity significantly. In contrast, during open surgery or hand-assisted laparoscopic surgery, the surgeon has the ability to easily grasp, retract, and manipulate organs as necessary. Typically, the surgeon's non-dominant hand is used mainly to retract, palpate, and expose tissue, while the dominant hand manipulates instruments to conduct surgical dissection.
Laparoscopic, single incision, natural orifice and robotic approaches each hold their own appeal. However, they lack the ability to manipulate organs as easily as the human hand. Advances in minimally invasive surgical techniques require new tools with increased functionality of the end effectors. Multifunctional tools with greater dexterity than those currently available are highly desired.
To address this need, Fraunhofer CMI designed, fabricated, and tested the first prototype of a laparoscopic tool that provides the dexterity of a hand. The "hand" has two jointed fingers and a jointed thumb attached to a laparoscopic sheath that can be collapsed to fit through a 12 mm trocar or small orifice. The handle provides control for three independent degrees of freedom: finger motion (bending/spreading), finger tip bending, and thumb bending. The tool can be used for pinching, grasping, and spreading motions. Furthermore, the thumb is "double jointed" so that the tool can be converted to a rake configuration to allow lifting motions. The initial prototype has been tested in a cadaver lab to demonstrate its utility. The "Lap-Hand" was used to complete standard surgical tasks in a simulation device in a time comparable to open and laparoscopic approaches, including "bowel" manipulation and peg movement. Cadaver testing confirmed the ability to grasp, elevate and move liver, stomach, colon and small bowel in a fashion expected by the hand. During the cadaver testing, various surgeons tested the device for its ability to grasp, elevate and move liver, stomach, colon and small bowel. Three surgeons, who had not had any prior training in its use, tested the device. No adverse events were noted and no bowel injury or perforation resulted from over-grasping. Use of such tools could both reduce the number of hand-incisions required and potentially transition more patients to undergo their abdominal procedures laparoscopically.
For more information, please contact:
Dr. Andre Sharon,
Executive Director
Fraunhofer Center for Manufacturing Innovation
asharon@fraunhofer.orgSOURCE: Fraunhofer USA News
-
Fighting H1N1 with Tobacco Plants: Project earns Joseph von Fraunhofer Prize for ENG's Sharon
June 11, 2013 • by Amy Laskowski | Boston University // BU Today
After decades of demonization as a health menace, the tobacco plant is about to become a source of potentially lifesaving medicines, thanks in part to the work of Andre Sharon, who leads a team that built a fully automated factory that uses synthetically altered tobacco plants to grow vaccines for some of the world's most deadly viruses, including H1N1, yellow fever, and malaria, as well as for emerging biological threats.
Those efforts have earned Sharon, a College of Engineering professor of mechanical engineering and the director of the Fraunhofer USA Center for Manufacturing Innovation (CMI), based at Boston University, the 2013 Joseph von Fraunhofer Prize. The prize was presented yesterday in Hannover, Germany, at a gala attended by German Chancellor Angela Merkel.
The 50,000 euro ($66,065) prize is given annually to a staff member of Fraunhofer Gesellschaft in recognition of outstanding scientific work leading to the solution of application-oriented problems. Sharon shares the award with colleague Vidadi Yusibov, the executive director of the Delaware-based Fraunhofer USA Center for Molecular Biotechnology (CMB) and a senior research fellow at the Delaware Biotechnology Institute. Fraunhofer Gesellschaft is Europe's largest applied research organization, with 66 branches worldwide and 8 in the United States. This is the first time in the award's 35-year history that it has gone to an American.
"This recognition is quite meaningful, because our work is going towards solving a real need in our society—the rapid production of vaccines," says Sharon. "It's a very great honor and very exciting."
The Center for Manufacturing Innovation, a collaborative center between BU and Fraunhofer Gesellschaft, was established in 1995. The center scales up promising research into real automation systems, laboratory procedures, instruments, and devices that are often deployed to the marketplace. CMI joined forces with the Center for Molecular Biotechnology in 2010 to build the plant-based factory, which is in Newark, Delaware.
Typically, flu vaccines have been produced in chicken eggs, in a process that Sharon says is expensive and perilously slow in the case of epidemics. "A good example of that was the H1N1 pandemic—the swine flu," Sharon says. "It took way too long to come up with a vaccine in the quantities required."
In 2009, in response to the H1N1 pandemic, which killed more than 150,000 people, the federal government began a $1.6 billion program—the most ambitious immunization campaign in US history—to find ways to quickly produce a large number of vaccines. The next year, the government's Defense Advanced Research Projects Agency learned of the work being done by the CMI and CMB, which uses tobacco plants' genetically engineered mechanisms to produce proteins within its leaves and stalks, and awarded the group a grant to study the rapid production of vaccines.
The collaboration now grows tens of thousands of tobacco plants in its Delaware factory, where they are tended by robots that bring the trays to and from the lighted, irrigated growth modules. After four to six weeks of growth, the robots move the plants to a machine that inserts genetic instructions to produce the appropriate protein. One or two weeks later, a harvesting machine shears the plants from their trays and uses routine chemical separation procedures to extract the protein, which is converted to a vaccine.
"This factory turned what would be an agricultural process—where you would have to seed the plants and give them the right light—into an industrial process, where you grow the plants hydroponically in trays, meaning they are not grown in soil," Sharon says. "These plant vaccine factories can be built anywhere in the world where a large number of vaccines are needed, whether it be urban, rural, or developing areas."
For Sharon, the Joseph von Fraunhofer Prize is confirmation of a rewarding career, one that has given him the opportunity to work in different areas. At BU, Sharon's research interests range from biotech and biomedical instrumentation to harvesting wave energy from the ocean.
"I have the best job in the world, because not only do I get to work with really smart and energetic faculty and students, I also get to work with industry," he says. "I have a foot in many areas because the research we do is translational, including biology and engineering, and it goes all the way to application."
Set Bookmark